Freedommachine
Active member
I have to make 200 of these assemblies. The center piece will likely be made from low carbon steel, seamless hydraulic tubing.

The small plug on the right gets fixed flush into the end of the tube. I was thinking of brazing them. I have very little experience brazing - to my inexperienced mind this looks like a good application for it and a good opportunity to gain some experience. To clarify, I'm talking about a brazed solder joint, not tig brazing.
Based on the numbers from my AWS brazing handbook, I know the application will be well under the yield strength for this type of weld.
The piece on the left; I was planning to tig weld the end with ER70 in a joint prepared like this:
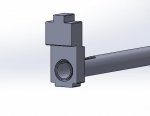
I cannot go into too much detail on the application of this assembly so my questions are more related to material weldablity and production efficiency. I have some technical knowledge but very little hands-on experience with production welding.
Is there a free machining steel similar to 12L14 but without lead that I could use in this application?
Is 12L14 as horrible to weld as the internet claims? I could use 1018 if necessary but I was hoping for something with a bit better machinability if possible.
Is my approach to welding these components reasonable from an efficiency standpoint?
Thanks.

The small plug on the right gets fixed flush into the end of the tube. I was thinking of brazing them. I have very little experience brazing - to my inexperienced mind this looks like a good application for it and a good opportunity to gain some experience. To clarify, I'm talking about a brazed solder joint, not tig brazing.
Based on the numbers from my AWS brazing handbook, I know the application will be well under the yield strength for this type of weld.
The piece on the left; I was planning to tig weld the end with ER70 in a joint prepared like this:
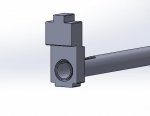
I cannot go into too much detail on the application of this assembly so my questions are more related to material weldablity and production efficiency. I have some technical knowledge but very little hands-on experience with production welding.
Is there a free machining steel similar to 12L14 but without lead that I could use in this application?
Is 12L14 as horrible to weld as the internet claims? I could use 1018 if necessary but I was hoping for something with a bit better machinability if possible.
Is my approach to welding these components reasonable from an efficiency standpoint?
Thanks.