I have been storing Cat40 and Cat50 toolholders in Tennsco metal cabinets, but they are not stout enough for the weight. A shelf buckled so time for an upgrade.
A couple weeks ago I picked up a pair of 36W 24D Stronghold cabinets at auction.

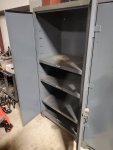
Last week I ordered 216 Heyco 2417 bushings for Cat40 and 160 Heyco 2424 bushings for Cat50. I got the bushings from Mouser for around $350 total ( a lot of bushings!)

Initially, I was planning to cut holes in the original shelves. I decided it's much less work to make new shelves.
I spaced the holes for 40 Cat50 per shelf and 54 for Cat40.
Four shelves per cabinet for toolholders and the bottom shelf for tools and pullstuds.
Price shopping laser vendors at the moment.
I'm considering powdercoating the shelves a bright color. Figure I best do it before they go in or I'll never Unload them to do it later.
A couple weeks ago I picked up a pair of 36W 24D Stronghold cabinets at auction.

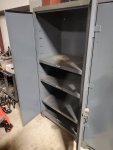
Last week I ordered 216 Heyco 2417 bushings for Cat40 and 160 Heyco 2424 bushings for Cat50. I got the bushings from Mouser for around $350 total ( a lot of bushings!)

Initially, I was planning to cut holes in the original shelves. I decided it's much less work to make new shelves.
I spaced the holes for 40 Cat50 per shelf and 54 for Cat40.
Four shelves per cabinet for toolholders and the bottom shelf for tools and pullstuds.
Price shopping laser vendors at the moment.
I'm considering powdercoating the shelves a bright color. Figure I best do it before they go in or I'll never Unload them to do it later.
Last edited: