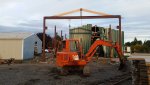
Uprights are 8x8 3/8 wall tube 22' long. Roof beams are 35' W14 48's Each footing is 5x5 18" thick
I built six of the 40" tall lattice girders laying in the foreground. That was the most time consuming part as they had to be very straight to work as intended. The green scabby looking building in the background is a 36' wide wood building I built within a month of closing on this place so I had a place to put stuff. I didn't like it so I tore it down. I recycled 100% of it. The trusses were all reused. All the 12' 2x6's got cut down to 10' and used in the roof of the new building. The green tin went on some of the interior walls. One thing to keep in mind was this was built with a shoestring budget and all the huge pieces of this building were built in that little space inside that green building you can see where 2 3ft wide panels are removed. That space was barely 8ft by 20 ft. I couldn't even get the forklift in there to flip stuff. It was mostly done by hand.
This picture has a lot going on. This is the Narwhale in action. It's an 11' mast extension I built so my little Komatsu could left things 26' in the air. Here is a 36' wood truss that has been removed from a pole building out of view and is being set in place into brackets mid-span on those 20' long lattice girders that were on the ground in the last pic.

This picture is about a month later around Thanksgiving time. The main roof is done. Assembling the roof purlins for the 15' "wings" down both sides of the building.

Here's setting the crane in place a couple weeks ago. That 14 x 20' opening has been temporarily walled off for a couple years while I collected the right pieces to build the doors. I had to open it back up to shuffle machines so figured I'd better get off my ass and get some doors built.
The door frame is 3 x 8" 1/4 wall tubing. The skin is cut from one 8 x 20' sheet of 3/16" hot rolled. The upper 6 feet of both doors is rolled steel casement windows with patterned glass removed from a 1910 building about 3 miles away in my town.
When I start assembling the doors I will add some pictures.
Oh, and the siding I used is structural metal insulated panels. They lock together air tight and rated for R20 value. I bought 100 16' long 3' wide panels left over from a Casino build up in Washington. That's why the building looks like it does. I had to build the biggest thing I could using the panels I had. I think they're about $350 a panel when you order new with a several month lead time. I offered the seller exactly what I was going to spend on 29 gauge steel barn siding and he accepted.