I have one machine that has gotten pretty bad over the last 1.5 weeks. every time it changes directions it leaves a coin/dwell mark. what causes this. I was thinking it was thrust bearings, a tech mentioned drawbar issues.
this part is roughed leaving .008 for a finish pass, the part pictured is after the finish pass. we ran these exact parts and exact program 4 weeks ago with no issues had few very small marks maybe a few tenths deep. tumbler took them right out. the new job we started last week, 1st 2 days no issues then it got much worse as the week went on. so ended up reprogramming the part so the endmill changes dir off the part
went to the second side today its getting worse about .002+ deep dwell marks.
the machine repeats all day long all axis's.
popped a indicator have about .0005 play when I move head with alot of force by hand, tried just moving tool in holder and the same .0005. (waiting on tech to stop by and check draw bar force.
that all being said a new endmill was used as well as the old endmill 1/2 s-carb sharp corner made no different. I dotn get the coining on the 1/4" or 1/8 endmills. Material is alum 6061 .
changed the program so it runs a rad on every axis change and slowed up the speed its more visual now maybe a few tenths deep at the most. while that does get the part working it doesnt fix the machine, I'm sure its mechanical.
maybe could be feed back bleed on the z axis motor when the x and y are moving??
the older fadal doesnt do it and the hass does it once in a blue moon but its only visual not more than a tenth id that.
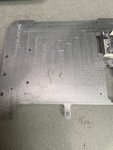

this part is roughed leaving .008 for a finish pass, the part pictured is after the finish pass. we ran these exact parts and exact program 4 weeks ago with no issues had few very small marks maybe a few tenths deep. tumbler took them right out. the new job we started last week, 1st 2 days no issues then it got much worse as the week went on. so ended up reprogramming the part so the endmill changes dir off the part
went to the second side today its getting worse about .002+ deep dwell marks.
the machine repeats all day long all axis's.
popped a indicator have about .0005 play when I move head with alot of force by hand, tried just moving tool in holder and the same .0005. (waiting on tech to stop by and check draw bar force.
that all being said a new endmill was used as well as the old endmill 1/2 s-carb sharp corner made no different. I dotn get the coining on the 1/4" or 1/8 endmills. Material is alum 6061 .
changed the program so it runs a rad on every axis change and slowed up the speed its more visual now maybe a few tenths deep at the most. while that does get the part working it doesnt fix the machine, I'm sure its mechanical.
maybe could be feed back bleed on the z axis motor when the x and y are moving??
the older fadal doesnt do it and the hass does it once in a blue moon but its only visual not more than a tenth id that.
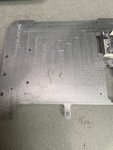
