Because you have to traverse the saddle outward to cut Internals and this causes the spindle to "pre-load" along some of the rack teeth on the spindle, effectively removing some of the available stroke length. If you traverse the saddle back and forth, you will see the spindle move up or down approximately that 1/2".
Thanks. Looking at it in person it makes perfect sense why the internal stroke is shorter.
This is a strange deal. I looked at the shaper this morning and I have mixed feelings about it. It looks way worse in person than the pictures. It's been in an open air breezeway in front of the guys home shop for a decade or so. Some rust, most of it looks OK, but it's not under power, it's 480 only, his "acre feet" of tooling he claimed to have is a handful of shaper cutters, a beyond fucked straight guide set for a #6, a helical set for a #6, a helical set for a #7 and a couple dozen large non-standard hobs.
He keeps calling the machine a #6, but it's a #7 with 725A stamped right in the face. The accessories he has are mostly for a #6 and don't even fit this machine. Like the extension arm for internal is way too small to fit this machine. He was telling me the coolant pump is missing and I'd need to rig up an electric one, but when I crawled back behind it the coolant pump and belt is all there. Not that it matters much, just kinda painting a picture of a guy who can't remember what any of this stuff is.
Initially, when I met this guy 9 months ago he offered me the (nice) shaper and hundreds of cutters, hobs and several guide sets for $2500. Today the price was $3000 for just the bare (not so nice) shaper.
I was able to test if an example of a part I want to cut internal splines in would fit and I'm now 100% sure a #7 fellows will do all the parts I have in mind which is neat.
The guy's also willing to help me out if I need any assistance. Not sure he's offering much there given he can't remember what machine he's selling or where all the tooling went.
I'm thinking.
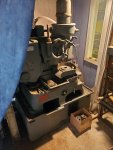
